Prior to application the steel must be cleaned by sand blasting to near white metal SSPC-SP 10 commercial blast cleaning SSPC-SP 6 or white metal SSPC-SP 5. In its simplest form the process consists of five stagestwo chemical stages and three water-rinse stages.
Lighter Manufacturing Process Our Craftsmanship Sarome Tokyo Cigarette Lighter And Accessory Brand
A process known as the Cronak process is used to create zinc chromate for use in industry.
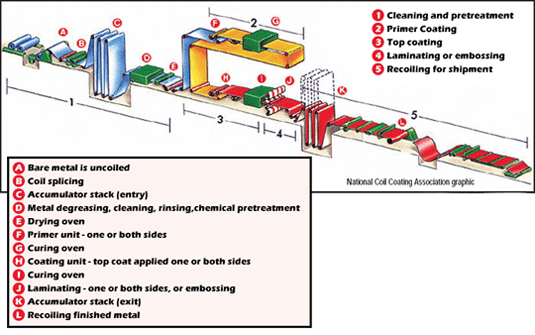
Zinc painting production process. Belgian-type horizontal retorts were operated in Britain as the main zinc-producing process for about 100 years starting in the mid-19th century. EPM-E Zinc oxide EPM-E is a direct or American process zinc oxide which is produced by a reduction-oxidation process followed by a special treatment resulting in a high quality zinc oxide. The result is a high-quality zinc oxide with low lead and cadmium content which is particularly needed in industrial applications.
50 Economic evaluation 51 Costing for sample A. This process is done by putting zinc or a zinc plated metal in a solution of sodium dichromate and sulfuric acid for a few seconds. Prior to beginning the zinc phosphate coating process the parts are thoroughly cleaned of oil grease wax dirt scale and other foreign matter and will not show visible signs of red corrosion products.
It is a very cost-effective process and is mostly used to provide a protective coating to metallic substances such as nuts bolts fasteners automotive parts and many other hardware items. Zinc oxide EPM is a direct or American process zinc oxide which is produced by a reduction-oxidation process. Zinc smelting is the process of converting zinc concentrates ores that contain zinc into pure zinc.
Authored by Bernardo A. Iron because in contrast zinc has a low boiling pointAt temperatures typically used for smelting metals zinc is a gas that will escape from a furnace with the flue gas and be lost unless specific. Th e batch hot-dip galvanizing process also known as general galvanizing produces a zinc coating on iron and steel products by immersion of the material in a bath of liquid zinc.
The paints are applied by brushing or spraying onto steel cleaned by sand-blasting. A protective zinc coating can be applied to articles by painting provided the volume fraction of the zinc dust or powder in the dry paint film is high enough to allow electrical contact from particle to particle and to the steel substrate. Zinc smelting has historically been more difficult than the smelting of other metals eg.
The daily output of each retort was about 40 kilograms 90 pounds and several hundred retorts were banked together and fired by gas. Zirconium is not regulated as a hazardous metal in North America or Europe. Phosphate conversion coating is a chemical treatment applied to steel parts that creates a thin adhering layer of iron zinc or manganese phosphates to achieve corrosion resistance lubrication or as a foundation for subsequent coatings or painting.
The first stage consists of melting the pure metal deposited on the cathodes during the electrolysis process and adding a controlled amount of copper and titanium in a series of induction furnaces to produce a liquid alloy. It places more sacrificial zinc on the surface creating more corrosion resistance. Other Benefits of Zinc Plating.
Zinc coating offers more than excellent protection against corrosion. 1 Pigment manufacturers send bags of fine grain pigments to paint plants. Zinc chromate can also be synthesized by using neutral potassium chromate K 2 CrO 4 and zinc sulfate ZnSO 4 which forms a precipitate.
Zinc plating can also serve as a protective undercoating prior to painting as it can promote greater paint adhesion. Zinc painting commonly referred to by the misnomer cold galvanizing is the application by brush or spray of zinc dust mixed with organic or inorganic binders. Today over 90 of zinc is produced hydrometallurgically in electrolytic plants.
The paint thus functions both as a barrier coating and as a sacrificial coating. 2 Zinc can be produced by a process called froth flotation which is also used for reduction of copper and lead ores. The new coating can be applied in fewer total stages than a zinc phosphate process and fewer chemical stages than both zinc and iron phosphate.
High Grade HG 9995 and Special High Grade SHG 9999 of zinc. Before the coating is applied the steel is cleaned to remove all oils greases soils mill scale and rust. 36 Process flow diagram sheet for production of emulsion paint 37 Block flow diagram for production of emulsion paint 38 Formula for samples selection.
Zinc Painting Production Process. The zinc ingots may have different grades. Additionally zinc plating is used in the production of tanks armored personnel carriers and other heavy military vehicles.
Zinc electroplating is one of the most popular methods that is used all around for the purpose of electroplating. Zinc-rich paints typically contain 92-95 metallic zinc in the film of the paint after it dries. The deposited zinc is stripped off dried melted and cast into ingots.
There the pigment is premixed with resin a wetting agent that assists in moistening the pigment one or more solvents and additives to form a paste. It is one of the most common types of conversion coatingThe process is also called phosphate coating phosphatization phosphatizing or. This process involves grinding the zinc ore to a fine powder mixing it with water pine oil and flotation chemicals and then agitating the mixture to float the zinc to the surface.
40 Quality control test 41 Equipments for quality control test 42 Quality control tests and results.
Types Of Galvanizing And Other Zinc Coatings
Find The Right Coating For Every Zinc Die Casting Component
Life Cycle Assessment Lca American Galvanizers Association
Zinc Oxide Is In Your Paint Zinc Oxide For Paint Citra Cakralogam
Industrial E Coating Process Advantages Of Electrocoating Ppg Coatings Services
Guidance For Lifetime Of Zinc Only And Duplex Zinc Paint Systems 1 Download Table
Galvanized Steel Coil Gi Thickness 0 12 4 0mm Width 30 1250mm Zinc Coating 40 275g M2 Web Www Sino Steel Net Tel 86 Zinc Coating Galvanized Steel Galvanized
Zinc Painting Production Process American Galvanizers Association
How Paint Is Made Manufacture Making Used Components Composition Product Industry Machine
The Zinc Plating Process Sharretts Plating Company
The Paint Shop Porsche Leipzig Gmbh
Zinc Coatings American Galvanizers Association
Manganese Zinc Phosphate Coating Services Metal Coatings
Zinc Plating Vs Powder Coating Staub Manufacturing Solutions
Phosphate Coating An Overview Sciencedirect Topics
Zinc Phosphate Case Study Precoat Metals Centrasep
Galvanizing Recycling Galvanizers Association
Zinc Rich Paint American Galvanizers Association